A numerical method that predicts buckling shows the hull was at risk.
August 12, 2023: Added note by Wagner.
Following is Dr. Ronald Wagner’s latest analysis of the Titan submersible, which has been transcribed here with his permission. It has been edited for language and clarity.
In today’s video, I want to present the results of an imperfection sensitivity analysis of the Titan submersible.
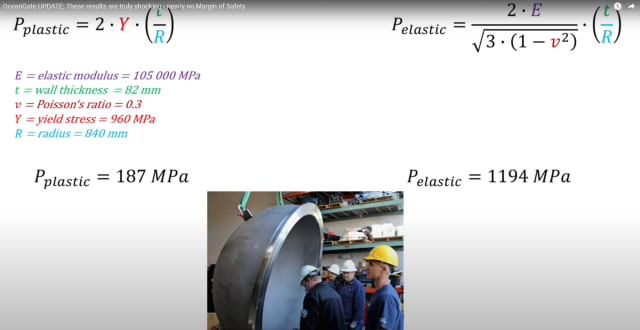
Here is the hemisphere. I have assumed some data points—elastic modulus, wall thickness, yield stress, radius, stress ranges and Poisson’s ratio. And if you use the equations for the plastic buckling pressure and the elastic buckling pressure, you basically get the results shown.

Elastic or plastic buckling?
The first point to be checked is if you have plastic or elastic buckling. That means that if you have plastic buckling, yield occurs before buckling, and if you have elastic buckling, yielding is not relevant.
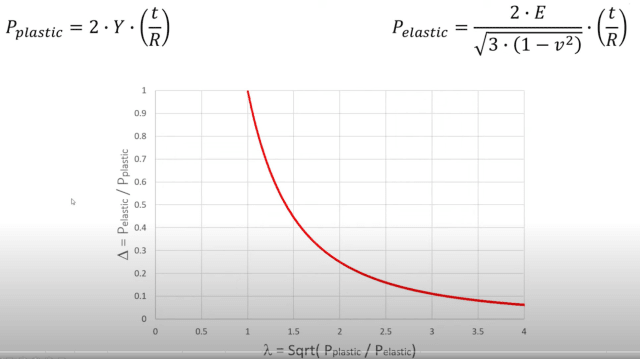
Therefore, we need to use this diagram so you can see on the horizontal axis we have lambda, which is the square root of the ratio of plastic and elastic buckling. On the vertical axis, we have delta, which is a ratio of elastic-to-plastic buckling pressure. Then we get the curve shown above.
The threshold between the elastic and plastic buckling is basically 1.73. And if we use the values for our hemisphere, then we get this lambda value [of 0.39] and it means the hemisphere buckles in the plastic range.
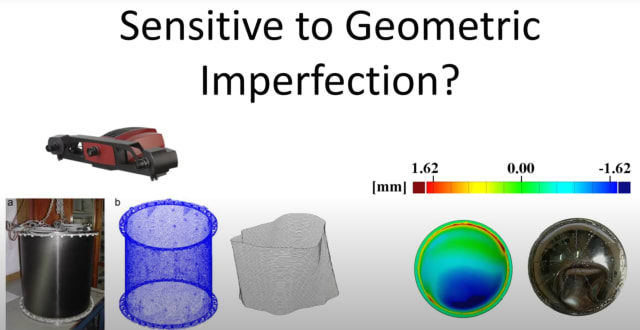
Now we want to check if it’s sensitive to geometric imperfections. Shapes are sensitive to geometric imperfections. What are geometric imperfections? You have an optical measurement system and your shell. Then you get a cloud of different measurement data points. You can increase the scale and compare it to a perfect cylinder.
[Added by Wagner] Amplitude of imperfection is 10% of cylinder thickness and real imperfections lead to more realistic collapse behavior.
In this case, we have introduced significant deviations. The same is also valid for spherical shapes.
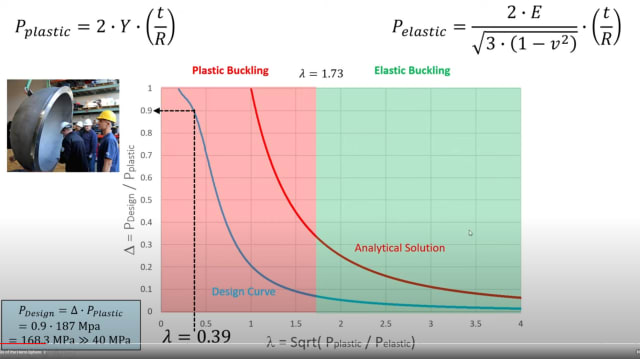
Therefore, we have a design curve. So that is another review solution. Blue is a design curve and if we use our lambda, we get to the design factor of 0.9.
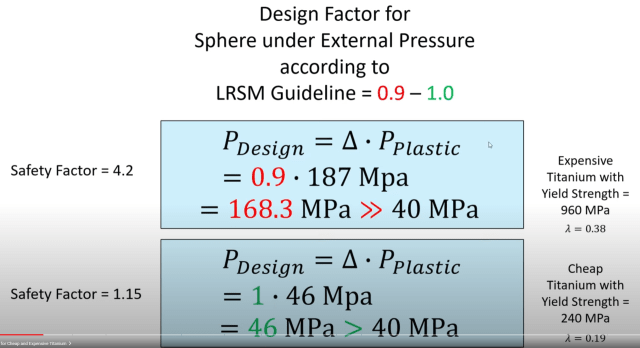
I have done this for expensive titanium and cheap titanium. I don’t know what was used [for the Titan]. It’s basically an assumption. With expensive titanium, we get a safety factor of 4.2, which I feel comfortable with. But if you use cheap titanium, there’s a safety factor of only 1.15, which I don’t feel so good about.
[Ed. note: Margin of safety is defined as factor of safety minus one. Therefore, a factor of safety of 1 is a margin of safety of zero, or no margin of safety.]
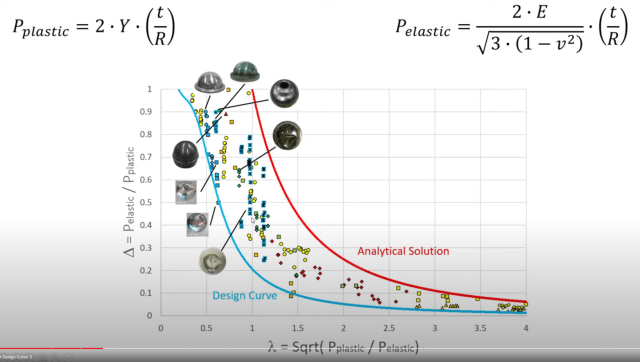
You probably asked, “Where does a design curve come from?” The design curve is based on a comparison of experimental data points. Each point is one test of a spherical shape. It’s basically a correlation of those tests.
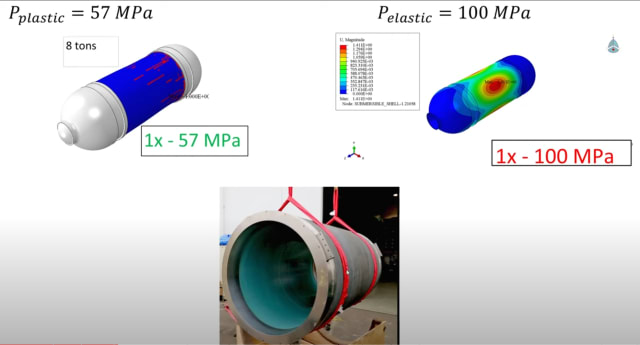
Now we come to the composite cylinder for the submersible. We have performed linear and nonlinear analyses because analytical equations are not really suitable for this problem.
We check again on whether we have elastic or plastic buckling. We have a lambda value [of 0.75] that is also below the threshold, so we can assume plastic buckling for material strength failure in the case of carbon fiber-reinforced polymer (CFRP).
Is the structure sensitive to geometric imperfections as well? And it’s not that easy, but I have taken a look at the NASA SP-8007 guideline for external pressure signals, and according to the guideline, there are two design factors (0.7 and 0.9), depending on the length of the cylinder.
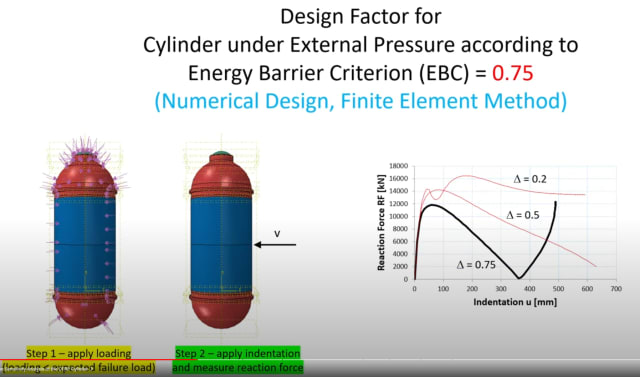
I have also performed a numerical imperfection sensitivity analysis using the energy barrier criteria. This basically looks like this. We have our shell structure to apply a loading [v, at the middle of the cylinder]. The loading is smaller than the expected loading and its increments. For example, 0.2 or 20 percent of the loading. Then we apply indentation so displacement and loads and measure reaction force.
This process is repeated until we find a function that looks like this. And then we have our design load.
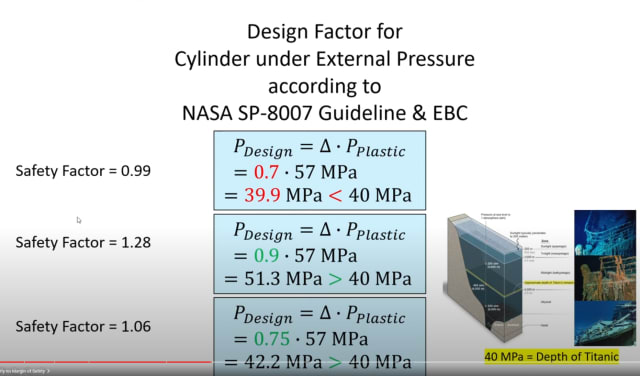
And now we come to the shocking end. So, if you use the NAS SP with P knocked down factors, or design factors, we get pressure values. We have to have a pressure value higher than 40 Mpa for the depth of the Titanic. And we can see here if we use 0.7, it’s not safe, and even if we use 0.9, it’s only marginally safe. If you use a numerical method [and 0.75], which I think is the most appropriate, you only get a safety factor of 1.06.
We have not even considered temperature differences, fatigue or wet material.
So, in addition, I performed the numerical analysis with geometric imperfections, and I want to show the results now.
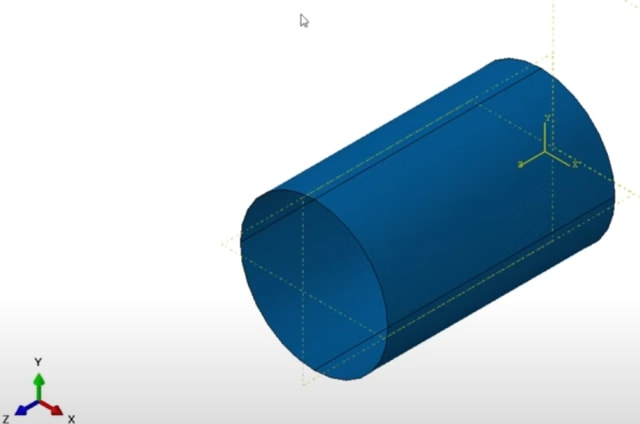
So here we have a perfect cylindrical shape. So, no imperfections. The section here looks perfectly circular. It’s perfect.
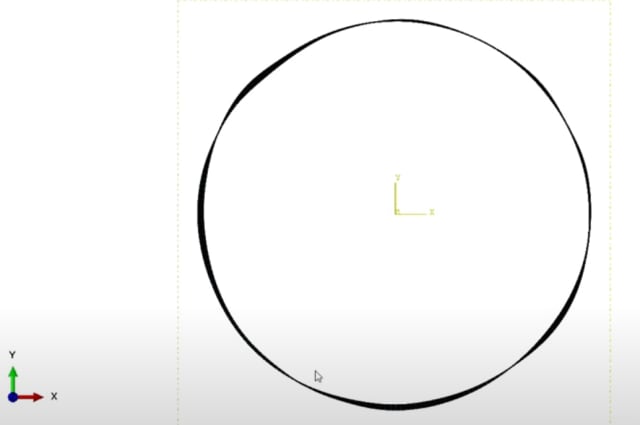
I added my imperfect model, and you can see the slight deviations in the section, slight symmetric imperfections. You don’t really see them in this view. But if we compare it with a perfect cylinder again
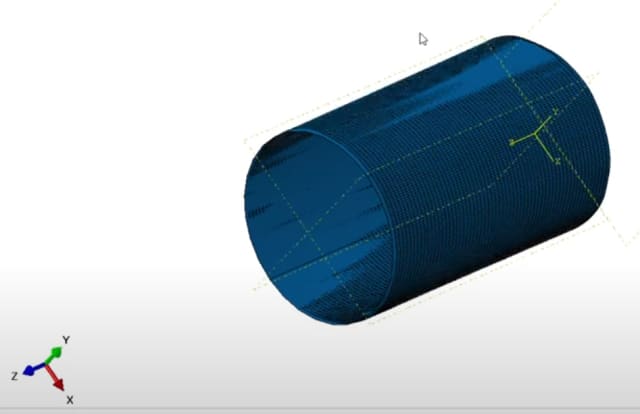
so here basically, you just see the deviations and also in the CD view, you’ll see that there are deviations from the perfect shape.
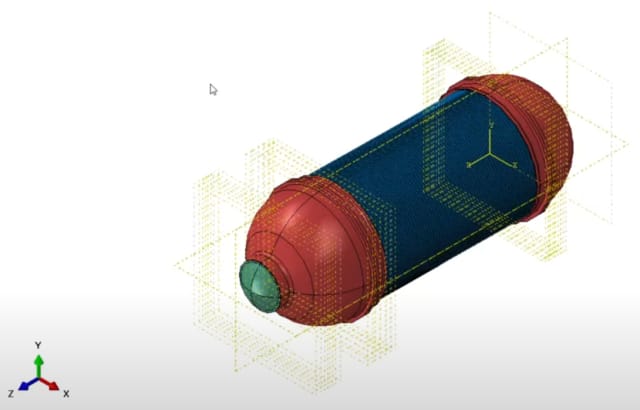
And then I have basically edited here the hemispheres. Okay, and I know I wish this was the result of this analysis.
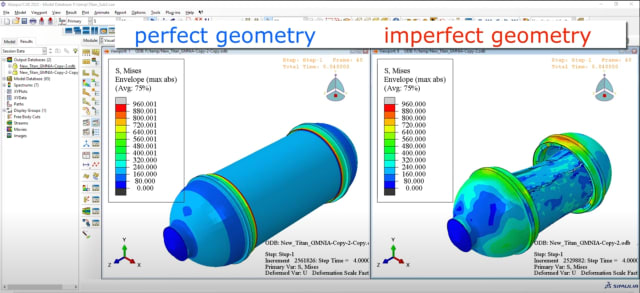
So, if you are asking how did I create an imperfect model? Go to my GitHub repository. There I have a folder that is called “Fourier_to_imperfection.” Here are many different imperfection measurements and a script, which you can use to transform the perfection to a certain geometry. You can download them all with the Download ZIP command. And it is based on this article. From this article, I have completed different manufacturing processes for composite and metal cylinders. There are imperfection signatures for composite levels and I have used one of the composite manufacturing signatures for the Titan module. There is a script that you can download the GitHub repository. I just edit the links, the radius, and the thickness, which is basically the imperfection amplitude. It is 10 percent of the thickness, so I think it is reasonable to assume an imperfection amplitude of 10 percent.
For the rest of the instruction on running your own Titan analysis and more about Ronald Wagner, you can pick up the YouTube video at this point with this link: https://youtu.be/bY_t16_PYEo?t=619
About Ronald Wagner
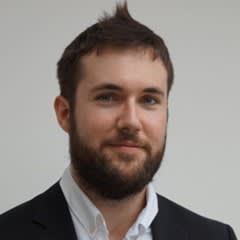
Ronald Wagner is a researcher, lecturer and an expert in shell buckling and material science. He has taught undergraduate and postgraduate students and is currently a Senior Research Engineer at the Digital Research Lecturing Program at the Technical University of Braunschweig, where he received a Ph.D. in mechanical engineering in 2018, While studying for his Ph.D, Wagner worked as a Research Engineer at the German Aerospace Center in Braunschweig. He earned a diploma in mechanical engineering from Otto von Guericke University of Magdeburg in 2013. Wagner has numerous peer reviewed publications but he may be best known for his YouTube channel, where he has several videos about the OceanGate submersible as well as on structural mechanics of thin shell vessels in general.
Next: Trust Me, I’m an Engineer—The Broken Promise That Sunk the Titan Submersible
Corrected August 14, 2023: Changed term in pressure formulae to (t/R) from (t/R)2