Design engineers know why supply chain data is so important.
A hundred years ago, the Ford River Rouge complex had everything it needed to turn raw materials into a running vehicle within one complex. Today, no manufacturing company would produce everything in one spot. Instead, they use a network of supply chains to procure components, parts and products. These modern supply chains are sophisticated and complex, but they enable companies to simplify their own internal processes. It’s great when it works; it quickly becomes a nightmare when it doesn’t.
Until recently, logistics professionals and procurement departments were some of the only people to worry about supply chains. However, recent disruptions fueled by global challenges, pandemics, climate change and geopolitical tensions have spotlighted the importance and fragility of these systems. Everyone from financial institutes, policymakers and the public quickly learned why a particular product became unavailable or expensive.
Consumer demand for sustainability, transparency and ethical production are other trends that have shone a light on supply chains. This has forced companies to reconsider their product development, operation and supply chain strategies to maximize their environmental, social and governance (ESG).
Traditionally, companies think about supply chain after products are designed and ready to be manufactured. However, recent research and experience shows that connecting development to the supply chains, via PLM systems, can avoid many challenges while saving time, materials and costs. In this article, I’d like to explore eight ways how mixing supply chain data with PLM systems can impact, innovate and expedite early product development.
The Ripple Effect of Product Design Choices
An engineer’s choices during product design ripple through development like a stone thrown into a pond. For instance, material selections can resonate throughout your entire value chain, influencing your financial outcomes. Grasping how modifications in design reverberate through business expenses enables smarter decision-making, manufacturing, product sustainability and supply chains.
In today’s dynamic market environment, product development cannot occur in a vacuum. To remain competitive and agile, companies need to integrate insights from every segment of their business into the design and development process. One key area that has often been overlooked in early product development is the supply chain. For instance, PLM has grown to support engineering and new product development in the form of improved design data management, collaboration and change management. This has played out in a recent survey made by the engineering analytics company CIMdata.
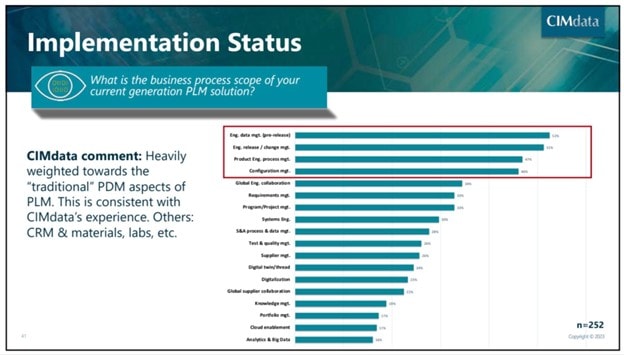
As a result, there is a big opportunity gap between connecting product design and PLM to downstream processes like manufacturing and supply chains. Making this information available to design engineers can unlock the potential of product development.
8 Product Development Impacts when Connecting PLM to Supply Chains
By providing detailed information about parts, suppliers, cost and many other aspects related to supply chain, engineers are getting a new source of intelligence that can be used in product design. By providing engineering data to suppliers and procurement, companies can mitigate supply chain risks and costly mistakes in the product development stage.
Here is how mixing supply chain data and connecting PLM systems with downstream processes and tools can impact and expedite early product development.
1. Informed Design Decisions:
By understanding the availability, cost and lead time of materials and components, design teams can make informed decisions that align with the realities of the supply chain. This can lead to designs that are not only innovative but also cost-effective and feasible to manufacture at scale.
2. Reduced Time-to-Market:
Having real-time insights into the supply chain allows development teams to foresee and circumvent potential procurement delays. By selecting components that are readily available or identifying alternative suppliers early in the process, companies can speed up product launches.
3. Enhanced Risk Management:
Supply chain data provides visibility into potential risks such as supplier insolvencies, geopolitical issues or potential bottlenecks. Early product development stages that take these risks into account can have contingency plans in place, reducing the risk of project delays or budget overruns.
4. Sustainability and Compliance:
Modern consumers and regulatory bodies are increasingly concerned about sustainability and compliance. Supply chain data can offer insights into the environmental impact of materials or ensure that components are sourced ethically. Integrating these insights into early product development can lead to products that resonate better with consumers and meet regulatory standards.
5. Streamlined Communication with Suppliers:
PLM systems can act as a bridge between development teams and suppliers. By integrating supply chain data into PLM, companies can facilitate better communication about design needs, material specifications or volume requirements. This ensures that suppliers are aligned with development goals.
6. Financial Predictability:
One of the significant challenges in product development is budget overruns. With accurate supply chain data integrated into PLM, companies can better forecast the costs associated with product development, leading to more predictable financial outcomes.
7. Quality and Performance Feedback Loops:
Supply chain data isn’t just about procurement. It also provides insights into product performance, warranty claims and return rates. This data, when integrated into the PLM, can provide invaluable feedback to development teams, guiding improvements in the next iteration of the product.
8. Strategic Supplier Relationships:
By integrating suppliers early into the product development process and sharing data through PLM systems, companies can foster stronger, more strategic relationships with their suppliers. This collaboration can lead to joint innovation, where suppliers suggest alternative materials or components that can improve the product or reduce costs.
Digital Thread and How to Make Connections?
The question remains: how can engineers make these connections between design and supply chains. What system and platforms can facilitate these connections and how do manufacturing companies adopt them?
One of the key trends in engineering and manufacturing software systems is to switch from old-fashioned “documents” to digital “data.” Until now, documents (CAD, derivative files, Excel BOMs and similar) were serving as a media transfer between multiple systems. This document paradigm has remained strong for the last 30-40 years, but it needs to change.
The strategy is to move from documents to data. Instead of focusing on how to export data into a “known format,” companies adopt digital platforms that use modern cloud technologies and data management systems.
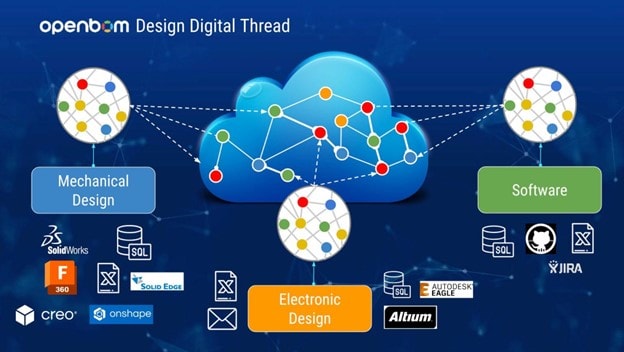
By capturing all engineering information into a digital thread and mixing this data with supply chain and procurement information, manufacturing companies can build product knowledge graphs to represent a unique set of data collections. This can intertwine data from both engineering, production and supply chain.
The technology of product knowledge graphs is a foundation for the future processes of creating data foundations for engineering, AI and PLM systems. These co-pilots, of a sort, will be capable of supporting engineers and manufacturing companies during their new product development process.
The integration of supply chain data into the early stages of product development through PLM systems is no longer a nice-to-have; it’s a necessity. In a world where agility, speed and innovation are key differentiators, companies that leverage these insights stand a better chance of success. Early product development, informed by real-world data, ensures that products are not just innovative, but also feasible, profitable and aligned with market needs.